Protective gloves can be divided into 3 categories depending on type and which risk or danger the gloves should protect against.
Category 1
Gloves of simple design, for minimal risks only
Example of gloves in this category are house-hold gloves used for cleaning and for protection against warm objects or temperatures not exceeding +50° C. Additional gloves in this category can include light-duty gardening gloves or other work where the risk for injury is minimal.
Category 2
Gloves of intermediate design, for intermediate risks
Gloves are placed in this category when the risk is not classified as minimal or irreversible. The gloves must be subjected to independent testing and certification by a Notified Body, whom then issues a CE marking showing the gloves protective capacities. In this category you will find general handling gloves requiring good puncture and abrasion performance according to EN 388.
Category 3
Gloves of complex design, for irreversible or mortal risks
Gloves in this category are designed to protect against the highest levels of risk e.g. highly corrosive acids. Gloves in this category must also be independently tested and certified by a Notified Body (approved by the EU commission).
EN 420
This standard defines the general requirements for protective gloves in terms of construction, fitness of purpose, safety, etc
The gloves themselves should not impose a risk or cause injury.
The pH of the gloves should be as close as possible to neutral.
Leather gloves should have a pH value between 3.5 – 9.5.
The highest permitted value for chromium is 3 mg/kg (chrome VI).
Specific details of any substance used in the glove which is known to cause allergies
Sized by reference to an agreed common European hand size, for example minimum length.
EN 388
Gloves giving protection from mechanical risks
Protection against mechanical hazards is expressed by a pictogram followed by four numbers (performance levels), each representing test performance against a specific hazard.
1) Resistance to abrasion
Based on the number of cycles required to abrade through the sample glove (abrasion by sandpaper under a stipulated pressure). The protection factor is then indicated on a scale from 1 to 4 depending on how many revolutions are required to make a hole in the material. The higher the number, the better the glove. See table below.
2) Blade cut resistance
Based on the number of cycles required to cut through the sample at a constant speed. The protection factor is then indicated on a scale from 1 to 5.
3) Tear resistance
Based on the amount of force required to tear the sample.
The protection factor is then indicated on a scale from 1 to 4.
4) Puncture resistance
Based on the amount of force required to pierce the sample with a standard sized point. The protection factor is then indicated on a scale from 1 to 4.
Volume Resistivity
This indicates Volume resistivity, where a glove can reduce the risk of electrostatic discharge. (Pass or fail test). These pictograms only appear when the gloves have passed the relevant test.
If some of the results are marked with a “X” means that this test performance is not tested. If some of the results are marked with a “O” means that the glove did not pass the test.
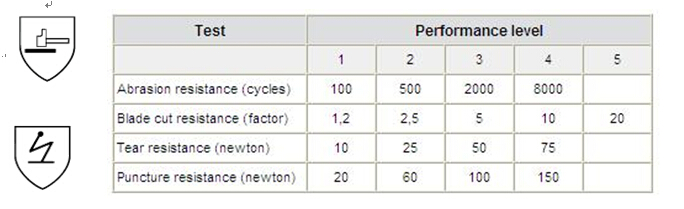
EN 407
Gloves giving protection from thermal hazards
The nature and degree of protection is shown by a pictogram followed by a series of six performance levels, relating to specific protective qualities. The higher the number, the better the test result. The following is tested:
1) Resistance to flammability
The glove’s material is stretched and lit with a gas flame. The flame is held against the material for 15 seconds. After the gas flame is distinguished, the length of time is measured for how long the material either glows or burns.
2) Resistance to contact heat
The glove’s material is exposed to temperatures between +100°C and +500°C.
The length of time is then measured for how long it takes the material on the inside of the glove to increase by 10°C from the starting temperature (approx. 25°C). 15 seconds is the minimum accepted length of time for approval. For example: to be marked with class 2, the glove’s inside material must manage 250°C heat for 15 seconds before the material exceeds 35°C.
3) Resistance to convective heat
The amount of time is measured for the heat from a gas flame (80 kW/m2) to increase the temperature of the glove’s inside material by 24°C.
4) Resistance to radiant heat
The glove’s material is stretched in front of a heat source with an effect of 20-40 kW/m2. The average time is measured for heat penetration of 2.5 kW/m2.
5) Resistance to small splashes of molten metal
The test is based on the total number of drops of molten metal required to increase the temperature by 40°C between the inside of the glove and the skin.
6) Resistance to large splashes of molten metal
Simulated skin is attached to the inside of the glove material. Molten metal is then poured over the glove material. The total number of grams is measured of how much molten metal is required to damage the simulated skin.
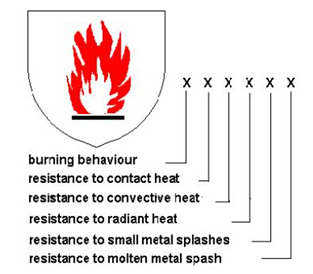
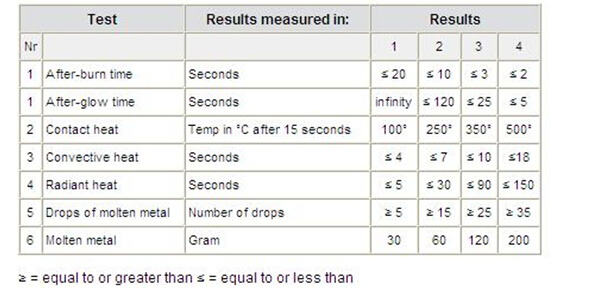
EN 12477
Welding gloves
This standard describes how the gloves are designed to provide protection for both hand and wrist while welding or simular work, this is a combination from testing EN 388 and EN 407.
Welding gloves shall provide resistance to small splashes of molten metal, short exposure to convective heat, to burning behaviour and to contact heat. The welding gloves shall give protection from mechanical risks as well.
Type A refers to gloves that shall provide a higher protection against heat.
Type B refers to gloves that provide a lower protection against heat but they are more flexible and pliable.
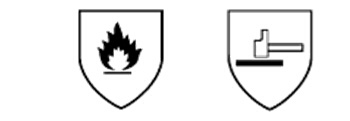
EN 511
Gloves giving protection from cold
Two things are measured with the glove:
1. How the glove’s material leads cold.
2. The material’s insulating capacity (with contact).
The last digit next to the pictogram shows if water penetrates the glove after 30 minutes. The pictogram will be accompanied by a 3-digit code.
The first digit show resistance to convective cold (performance level 0-4).
The second digit show resistance to contact cold (performance level 0-4).
The higher performance level, the better insulating capacity.
The third digit show permeability to water (performance level 0 or 1).
0 = water penetration after 30 minutes.
1 = no water penetration after 30 minutes.
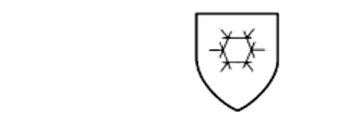
EN 374
Gloves Giving Protection from Chemicals and Micro-Organisms
In many countries there are more than 15,000 different chemicals in use in more than 60,000 products within industry, construction, agriculture etc. Tested and approved chemical gloves are the right solution against many of these chemicals.
You have to find out the name of the chemical and approximately how long time you need to be in contact with the chemical. Then we will help you to find the correct kind of glove.
The chemical gloves that are not approved according to EN 374-2004, but are approved according to the old EN 374-1994 have the pictogram (1). EN 374-1994 is still relevant. If the chemical gloves are approved according to EN 374-2004 has the pictogram (2).
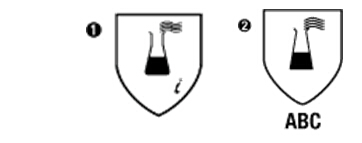
Scope
This standard specifies the capability of gloves to protect the user against chemicals and/or micro-organisms.
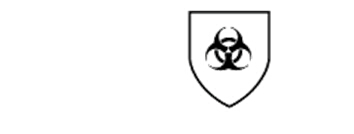
Definitions - The gloves length of life
Degradation - is rated according to the change in integrity following chemical exposure. The rate of degradation depends on which chemical the glove has come in contact with.
Penetration - is the flow of chemicals and micro-organisms through the porous material, seams, small holes or other small defects in the glove material.
Permeation - is the process where a chemical passes through the glove’s material on a molecular level.
Permeation means the following: a chemical’s molecules penetration through the outer material of the glove.
Diffusion is the movement of molecules through the material.
Desorption is the outward flow of molecules from inside the glove.
Requirements
Minimum liquid proof section: The minimum liquid proof section of the glove shall be at least equal to the minimum length of the gloves specified in EN 420.
Penetration: A glove shall not leak when tested to an air and/or water leak test, and shall be tested and inspected in compliance with the Acceptable Quality Level.
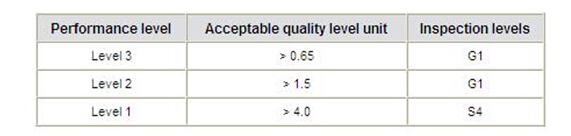
The ‘Chemical resistant’ glove pictogram must be accompanied by a 3-digit code. This code refers to the code letters of 3 chemicals (from a list of 12 standard defined chemicals), for which a breakthrough time of at least 30 minutes has been obtained.
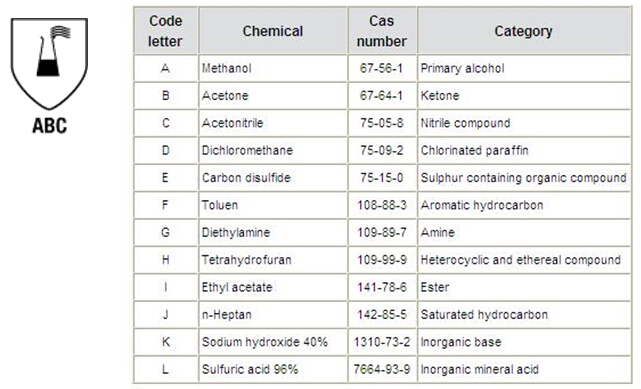
Permeation: Each chemical tested is classified in terms of breakthrough time (performance level 0 to 6).
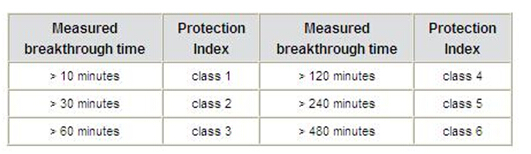
The ‘Low Chemical resistant’ or ‘Waterproof ’ glove pictogram is to be used for those gloves that do not achieve a breakthrough time of at least 30 minutes against at least three chemicals from the defined list, but which comply with the Penetration test.
The ‘Micro-organism’ pictogram is to be used when the glove conforms to at least a performance level 2 for the Penetration test.
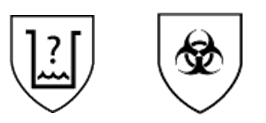
The chart below will help you select the right material suitable against different types of chemicals.
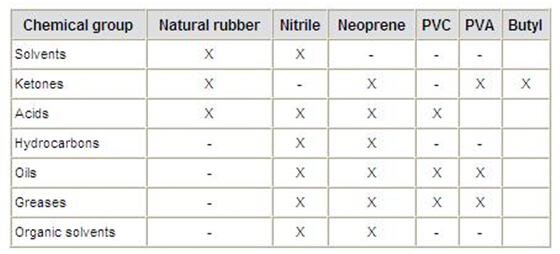
Warning: The chemical data information does not necessarily reflect the actual duration in the workplace.
EN 455
Requirements for single use medical gloves
This standard specifies requirements and tests for gloves for medical purpose.
EN 60903
Gloves giving protection from electrical risks
To protect yourself from electrical risks requires that you use special gloves. Gloves that are manufactured and approved according to EN 60903 are the only gloves that should be used when there is a risk for electrical shock.
To help in the decision as to which glove provides the best protection, it is important to know which
voltage level can occur.
Refer to the table below for a summary of which glove classes tolerate different voltage levels. To protect the electrical protection gloves against wear and tear, for example sharp cables, etc, a specially designed protective glove can be worn over the electrical gloves.
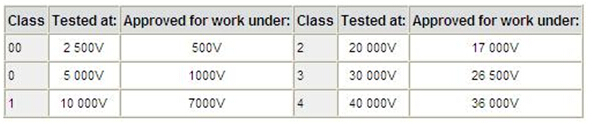
ESD
Electro Static Discharge
The human body is an excellent conductor of electricity. A person, who, for example, walks across a floor, removes a piece of synthetic clothing, or works at a desk, can become statically charged with upwards of several thousand volts. Somehow this static charge must be released. Sometimes this can result in an “electric shock”. In a large variety of industries, this discharge of static electricity can damage a variety of products. This is primarily true within the electronics industry where some components are very sensitive. Other examples are:
The automotive industry, where static electricity poses a fire-risk in the paint shop.
Chemical and pyrotechnics industries, where there exists a risk for explosions.
Laboratories, where precise measurements can be disturbed.
Static electricity can even lead to production disruptions within different industries. How, then, do you get rid of the electrical charge that you carry? It should be lead away with suitable ESD products, for example semi conductive work-benches, chairs, or flooring as well as those products you “put on” like clothes, shoes, gloves and armband. Some environments are classified as EPA, ESD Protected Area, which means that the whole work area is protected against static electricity. To prevent product damage from electro static discharge, every work environment should be designed based on the existing requirements for the use of various ESD products.